The tricks of the SM400 servo module
Following the Helvest philosophy, we have introduced some innovations in the SM400 servo module to make its operation more realistic and to eliminate some drawbacks that model railroaders sometimes encounter when using these useful motors. In this article we go into more detail about them.
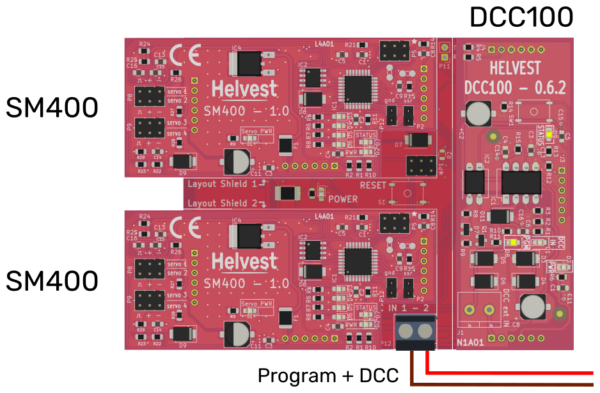
Configurable addressing
With all Helvest DCC decoders, each individual output can have an address independent of all others.
So if you fit a decoder with, for instance, 8 servos, like the one in the picture, it is possible to give servo 1 one address, say 36, servo 2 a completely different one, say 183, servo 3 yet another, say 1, and so on. Just write
in CV 120: the value 36;
in CV 130: the value 183;
in CV 140 the value 1 and so on.
This function is explained in detail in another article and has another advantage that is particularly useful for servos: if you want to move two or more motors at the same time, simply assign the same address to both outputs.
This can be the case, for example, with barriers at a level crossing, as shown in the illustration, which are connected to the outputs “Servo 1” and “Servo 2”. The barriers must of course move together, but the programming will not be complicated: simply assign the same address to output 1 (CV120) and output 2 (CV 130).
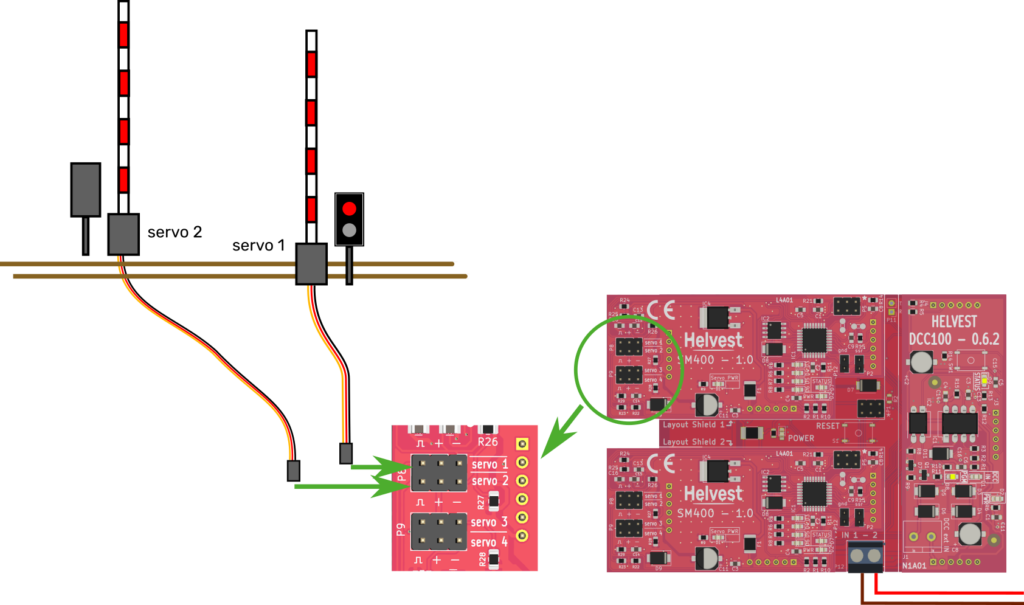
Position memory
The SM400 modules “remember” which position the servo was in. The system could be switched off or the power supply could fail due to a short circuit or some other reason. In this case, the motor remains in the position it was in at the time of the interruption.
This has two very important practical advantages:
1) If the power supply is interrupted intentionally or due to a fault or short circuit, the servos do not have to be checked again.
2) When starting the model railway, it avoids generating a high current by moving the motors together.
This increases the reliability of your layout in case of problems.
Current compsumption sensor control
Another new feature is the sensor that monitors if the motor draws too much current: If the motor is loaded beyond a certain value, the power supply is automatically interrupted.
This protects the mechanisms to which the motor is connected from being damaged in the first place if they are overloaded for any reason.
For example, if the motor is set incorrectly, it could overload and bend the barrier of the level crossing or the needle of a switch.
In addition, the reliability of the model railway is further improved: a motor that draws too much current can affect the power supply of other devices or decoders.
Thus, a problem with one motor does not lead to a malfunction of the entire layout, because the motor is temporarily excluded.
The intervention value of this control can of course be set for each individual output, with CV 126 (for servo 1), 136 (for servo 2), 146 (for servo 3)… up to 196 (for servo 8). A higher value increases the intervention threshold (i.e. the motor can apply more force before the control intervention), a lower value makes the control more sensitive (i.e. the amount of force at which the system interrupts the power is lower).
Of course, if for some reason you are not interested in this feature, you can exclude it completely for one or more outputs: write the value 255 in the CV(s) of the motors where you do not want it, and your motors can unleash all their power.